- Published on
NYU's Open Source RUKA Hand Promises High Dexterity on a Budget
- Authors
- Name
- The Editorial Team
- @humanoidsdaily
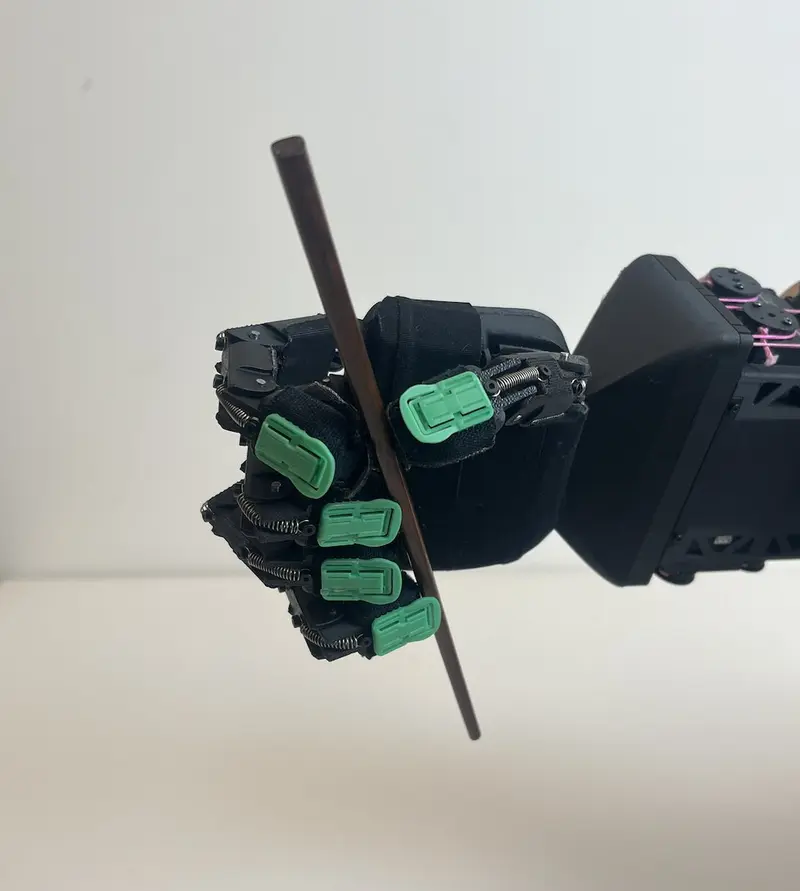
NYU Researchers Open Source RUKA: A High-Performance, Low-Cost Humanoid Hand
A new robotic hand developed at New York University aims to make dexterous manipulation more accessible. Dubbed RUKA, the five-fingered, human-sized hand combines 3D-printed parts with a learning-based control system, achieving impressive strength and dexterity at an estimated component cost of around $1,300. The entire project—hardware designs, assembly instructions, and control software—has been released open-source.
Rethinking Hand Design with Learning
Developed by a team at NYU's Computational Robotics Lab led by Prof. Lerrel Pinto, RUKA emerged from a multi-year effort to overcome traditional trade-offs in robotic hand design. Typically, achieving human-like dexterity, strength, and compactness involves expensive components and complex engineering. The RUKA project, detailed in a paper titled "RUKA: Rethinking the Design of Humanoid Hands with Learning," takes a different approach.
Instead of relying on intricate mechanics and numerous sensors, the team utilized tendon-driven underactuation, similar to human anatomy. This allows for a slimmer, more anthropomorphic form factor using fewer motors. The complexity shifts from hardware to software: a learned neural network controller manages the intricacies of the tendon system, compensating for factors like tendon elasticity and friction without needing direct joint sensors.
"We wanted a hand that could be human-sized and compact, yet strong, and built from affordable, easily replaceable parts," the researchers state on the project website. The open-source release aims to democratize access to capable research hardware.
Anatomy of an Affordable Hand
RUKA features 15 degrees of freedom across its five fingers, driven by 11 Dynamixel servo motors housed in the forearm to save space and manage heat. The finger joints are coupled—one motor flexes multiple joints via tendons made from high-tensile braided fishing line running through PTFE tubing. Passive extension is achieved using embedded springs, further simplifying the actuation.
Most structural components are 3D-printed using standard PLA for rigidity and TPU for compliant finger pads, allowing parts to be produced quickly on common printers. The hand closely matches adult human proportions (~18 cm length), enabling it to use standard data gloves and interact with everyday objects.
Notably, RUKA lacks onboard joint angle or tactile sensors. To achieve accurate control, the team developed a novel calibration method using an external motion-capture glove (like a Manus VR glove) to map motor commands to finger configurations. This data trains a recurrent neural network (LSTM-based) controller that acts as a learned inverse kinematics and dynamics model. An auto-calibration routine fine-tunes the model for each specific hand assembly.
Performance and Trade-offs
Evaluations show RUKA punches above its weight class. It reportedly lifted over 6 kg in a power grasp and demonstrated superior reachability compared to other research hands like the LEAP or Allegro hands. Its pinch force is around 2.74 N. Teleoperation tests showed fingertip tracking accuracy within about 3 mm, sufficient for tasks like operating a power screwdriver or using keys.
The design emphasizes durability and repairability. Its modular fingers can be swapped out in roughly 20 minutes, and tests showed it could operate continuously for over 20 hours without overheating. The use of inexpensive, replaceable parts encourages experimentation without fear of costly damage.
However, the design involves trade-offs. Underactuation means less independent control over individual finger joints compared to fully actuated hands, potentially limiting extremely fine manipulation. The reliance on a learned model and the lack of integrated sensors mean the system operates largely open-loop after calibration; unexpected events like object slippage aren't directly sensed by the hand itself. Performance depends on the quality of the initial calibration and the learned model.
While RUKA excels at general-purpose, human-like tasks, it's not intended for extreme high-force applications or tasks requiring sub-millimeter precision and delicate force feedback, where specialized grippers or high-end sensorized hands might still be superior.
Open Source Dexterity
By releasing RUKA as an open-source project, the NYU team provides a powerful tool for the robotics community. Its low cost and high performance could significantly lower the barrier to entry for advanced manipulation research and education.
The project serves as a compelling case study in co-designing hardware and software, demonstrating how machine learning can enable simpler, more affordable mechanisms to achieve complex behaviors. As the RUKA platform is adopted and potentially modified by others—perhaps incorporating tactile sensing or integrating with different robot systems—it could spur further innovation in making robots more capable of interacting with the human world.
The project's repository is found here: https://ruka-hand.github.io/